Scientists print robots with functional bones, ligaments, and tendons
The advancement in 3D printing technology has significantly broadened the range of materials that can be utilised. While the previous limitations revolved around fast-curing plastics, this new technique now enables the use of slow-curing plastics, which offer superior elasticity, durability, and robustness.
This breakthrough was made possible through the collaboration of researchers from ETH Zurich and a US-based start-up. By tapping into this innovative technology, researchers can now manufacture complex and long-lasting robots using a diverse range of high-quality materials. Additionally, the newfound capability to combine soft, elastic materials with rigid components opens up endless possibilities for creating delicate structures and parts with desired cavities.
The novel technology has allowed the researchers at ETH Zurich to achieve a first-of-its-kind feat: they successfully printed a robotic hand consisting of bones, ligaments, and tendons all made from different polymers in a single printing process. "With the fast-curing polyacrylates we used in 3D printing before, creating a hand like this would have been impossible," explains Thomas Buchner, the study's first author and a doctoral student in the robotics group led by Professor Robert Katzschmann at ETH Zurich. "Now, we employ slow-curing thiolene polymers, which possess exceptional elastic properties and quickly revert to their original state after bending, unlike polyacrylates." This makes thiolene polymers an ideal choice for fabricating the elastic ligaments of the robotic hand.
Moreover, the stiffness of thiolenes can be finely tuned to meet the specific requirements of soft robots. "Soft robots, such as the hand we developed, offer advantages over conventional metal robots. Their softness reduces the risk of injury when interacting with humans, and they are better suited for handling delicate objects," explains Katzschmann.
The traditional layer-by-layer approach used in 3D printing involves depositing viscous materials at each point, followed by immediate curing with a UV lamp. However, the previous method required scraping off surface irregularities after each curing step, which was only feasible with fast-curing polyacrylates. Slow-curing polymers, such as thiolenes and epoxies, would cause complications with the scraping process.
To overcome this limitation, the researchers took 3D printing to the next level by incorporating a 3D laser scanner that inspects each printed layer for surface irregularities in real-time. "A feedback mechanism compensates for these irregularities during the printing of subsequent layers by calculating precise adjustments to the amount of material to be printed," explains co-author Wojciech Matusik, a professor at the Massachusetts Institute of Technology (MIT). As a result, the new technology no longer requires the smoothing out of uneven layers, but rather seamlessly incorporates these irregularities into the printing process for the next layer.
About The Author
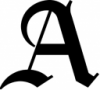
Welcome to Aryan Age, an English newspaper that has been serving readers since 2011 from Delhi. With a loyal circulation of over 19,000, we are dedicated to providing our readers with the latest news and information, as well as insightful analysis and commentary that help them navigate the complex and rapidly changing world.
Comment List